Posted 20 October 2021
Tim Harris, Technical & Support Services Manager of our sister company Cablecraft Ltd, discusses why it is important to achieve a quality crimp connection.
In the ever-evolving electrical installation market, some core requirements never change – the need for quality, reliable electrical terminations.
Whether it be through the application of solderless crimp terminals or the use of cord end ferrules inserted into a terminal block, the fundamentals are the same. Correct wire preparation, terminal selection and the right tooling, are 3 of the 5 key elements required to create a quality crimp terminal. Documentation and trained personnel make up the 5 key elements of the crimping system.
Matched tooling and terminals are required to achieve quality results that can be relied on. Correct tool and terminal selection at the point of design plays a vital role in ensuring that the job is done in the correct way first time. Without all the elements in place errors can be made resulting in wasted time, scrapped products and costly failures.
1. Wire Preparation
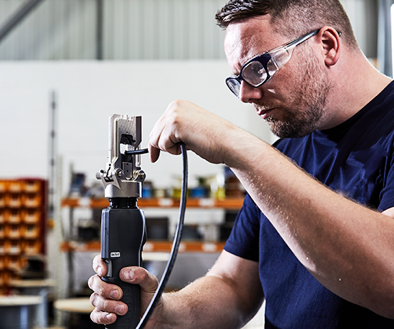
A key element to achieving a quality crimp is wire preparation. Good quality, well maintained tools will cut the conductor cleanly and avoid damage. Insulation material for cables can vary, so having the right tool for the job ensures that insulation is removed completely, and all the wire strands are kept intact. The temptation to use cable cutters should always be avoided and a specialist stripping tool should always be selected to complete the job.
During the stripping process up to 60% of strands can be removed or damaged thus reducing the carrying capacity of the cable, whilst also reducing the mechanical strength of the joint. Whilst this is less of an issue with single core cables any damage to the conductor can lead to problems with the electrical connection. Torn or ripped insulation can cause issues with the placement of the insulation support and wire barrel in the terminal. This is a problem as correct strip length is key for positioning of the wire in the terminal barrel. Selecting the right design of stripping tool with the correct blade shape, can greatly reduce the chance of mistakes being made and damage to the cable.
2. Terminal Selection
Selection of a terminal can be based on varying different factors including price, application, ease of use, specification and availability. Selecting quality terminals from reputable manufacturers gives contractors the peace of mind that the equipment is fit for purpose. All terminals should have the manufacturers name and sizing stamped on the terminal. This is vital for traceability and quality control after the terminal has been installed. Terminal suppliers should be able to provide technical data and drawings for all the terminals they sell and have recommended tooling to match each terminal. Insulation material and base metal needs to match the cable and time should be taken in selecting the correct product. While end ferrules are installed to contain the strands and are not the final termination of the cable, care still needs to be taken in the crimping of these products and quality manufacturers selected.
3. Tool Selection

Each tool has a set of dies which match the terminal in terms of size and form. The dies are designed to crimp the terminal to the correct size to ensure the wire barrel achieves the correct compaction and the insulation support is formed into the correct shape. Many tools come fitted with a terminal locator to help the user position the terminal in the correct place. Incorrect compaction through the use of unmatched tooling can lead to air gaps, which in turn can lead to overheating. The tools dies should also mark the terminal to state that is has been crimped with the correct size of die or the correct aperture in the tool head.
Crimp tools need to be maintained and kept in good condition. In many industries tool calibration is required and is an essential part of quality assurance. To prolong the life of the tool, we advise they are calibrated on a yearly basis to ensure they are performing to the correct standard. Along with the manufacturer’s instructions and terminal data, calibration certificates form the documentation element of a crimping system.
4. Documentation
Crimping systems were developed so repeatable results can be achieved and ensure quality results time after time. The BS EN 60352-2:2006 standard gives guidance on general requirements and test methods for quality assurance.
5. Trained Personnel
Trained personnel are key when creating a perfect crimp. We offer a full range of crimping solutions along with matched terminals and tooling, to achieve results that meet all the relevant industry standards. Crimp training courses are available and expand on the basics of the crimping process and quality control. All of the steps mentioned in this article go towards ensuring that a quality crimp can be produced. The information is not manufacturer specific and applies to all solderless crimp terminals. For more information on our crimp training course, please visit https://www.cablecraft.co.uk/cablecraft-crimp-training-course
Download the comprehensive guide to good crimping practice by clicking here.
Cablecraft Ltd, cablecraft.co.uk